Artec Space Spider和Control X解锁更快更精准的制造工艺
概要:多阶段制造流程会带来不确定因素和工艺偏差,导致最终结果不准确。若没有合适的工具和系统性方案,纠正调查难度不小。
目标:使用Artec 3D Space Spider和3D Systems的Geomagic Control X计量与质量管理软件,通过最低迭代率,降低总成本与项目时间,提升准确度,效果远超铸造厂预期。
使用工具:Artec Space Spider, Artec Studio, Geomagic Control X
扫描与监测增材制造部件可降低成本,减少迭代,提升准确度和质量水平。
随着全新生产技术的出现,制作优质零件也随之产生了新的技术难题。通常,在合同制造商初次生产时,就要先对全新工艺进行重要调整,以了解收缩、表面处理和重复性等情况。增材制造也不例外,但追踪这些生产方式的工具水平还很落后。但现在开始,一切都有了改变。
多数制成品的生命周期和生产流程往往遵循一个共同流程。设计、制造、检验是工艺、步骤和职责方面考量的普遍做法。每个阶段都影响着生产零件的品质。根据制造部件的复杂程度及特性,真正的工艺流可能需要多次循环调整和反馈。
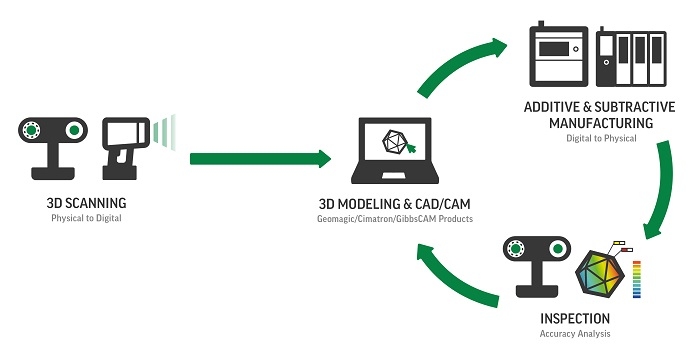
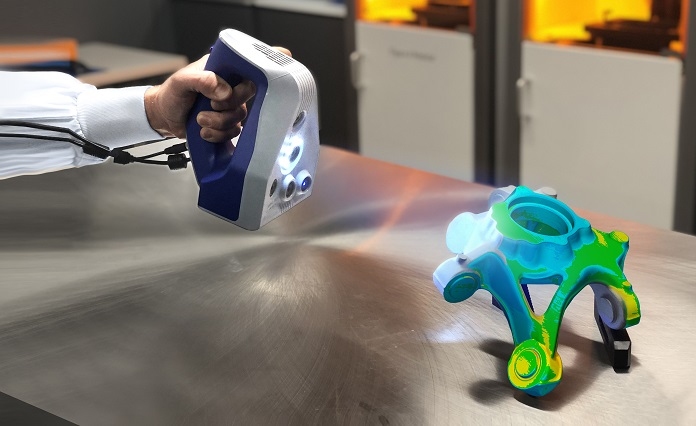
在下方工艺流案例中,我们展示了配合使用Artec Space Spider与Geomagic软件,可在设计、生产验证、制造流程的所有阶段,完成3D打印蜡型铸件及其部件的全外形捕获与分析。
挑战
多阶段制造流程会带来不确定因素和工艺偏差,不断累积会导致最终结果不准确。如果没有合适的工具和系统性方案,纠正调查难度不小
解决方案
Artec 3D Space Spider扫描仪和3D Systems的Geomagic® Control X™计量与质量管理软件
结果
• 采用3D扫描和检验网调整增材制造无工具制模流程,通过最少迭代(1次),提升效果
• 降低27%的成本,准确度提升10%
• 与铸造厂密切合作,分析制模流程网,少量迭代(1次),但最终部件效果远超铸造厂预期
• 最终部件准确度提升14%
• 表面处理成本降低,无需二次加工工序

Artec Space Spider是一款带超高分辨率的手持式3D扫描仪,能精确捕获小型物体和复杂几何,并用于尺寸检查。
Space Spider即开即用,扫描过程轻松,无需复杂的前期准备或大量使用培训,用户可在任何地方完成数字化操作。Artec 3D的“无标靶”专利算法能单独依靠扫描仪捕获物体外形与色彩,无需在物体上增加任何标记。
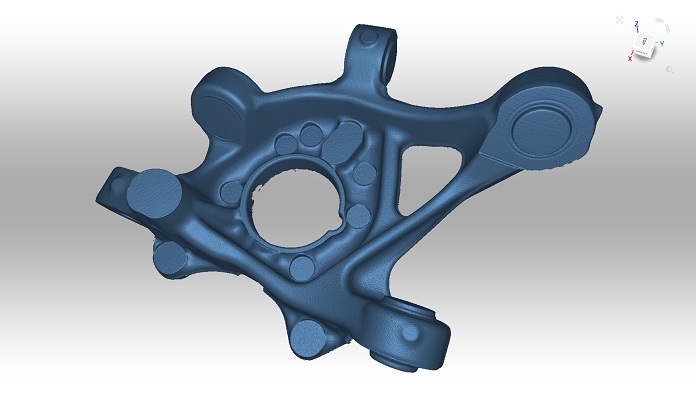
Artec Studio扫描软件
3D Systems的Geomagic Control X是工业级计量软件,能为制造工艺进行根本原因分析和修整,与3D扫描原生软件相同,Control X是理想的便携式测量设备。Control X可以让所有团队成员在任何地方实现更快、更多、更完整的测量。
整套解决方案为复杂制造工艺的顺利生产提供了独特方式。结果如何呢?大幅提升了最终部件的整体质量、准确度和再现性。
设计
在该制造案例中,我们重复了客户的一项真实项目,但简化了部分细节。在本案例中,我们的客户需要研发一辆特别的轻量型自动驾驶汽车。为加快上市时间,选择了目前市面上许多汽车部件与系统,结合起来完成汽车原型。在这过程中,他们找到了一款特殊的转向节,对项目颇有用处,客户需要对其数字化,捕获设计,用于轻量材料的设计修改与生产。
首先,对原始件进行3D扫描和逆向工程。Artec Space Spider被用于产品快速数字化,并通过独特的混合建模技术,在Geomagic Design X中完成准确建模。通常,客户会在按完工图(准确度高)或设计意图(尺寸优先)两种建模方式中选择。混合建模法结合了两种方式,完成的CAD实体模型既包含尺寸特征,也包含高度准确的NURB曲面。通过这种方式,不到1.5小时就完成了建模,随后以基于特征的CAD直接实时导出至SOLIDWORKS。
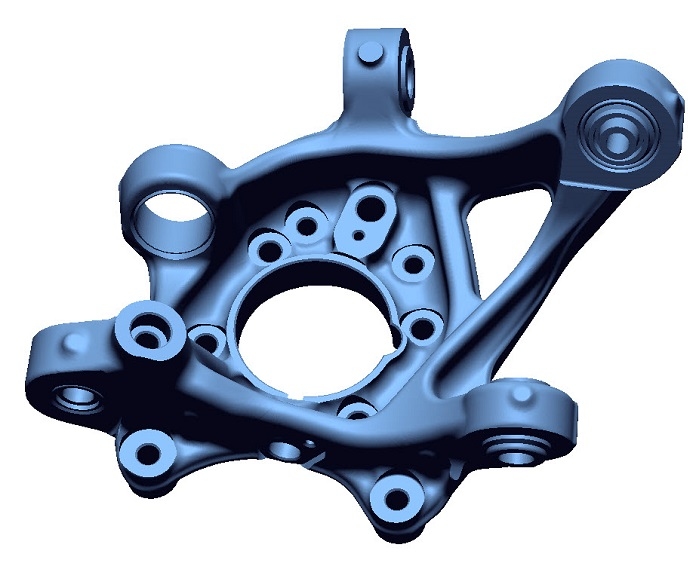
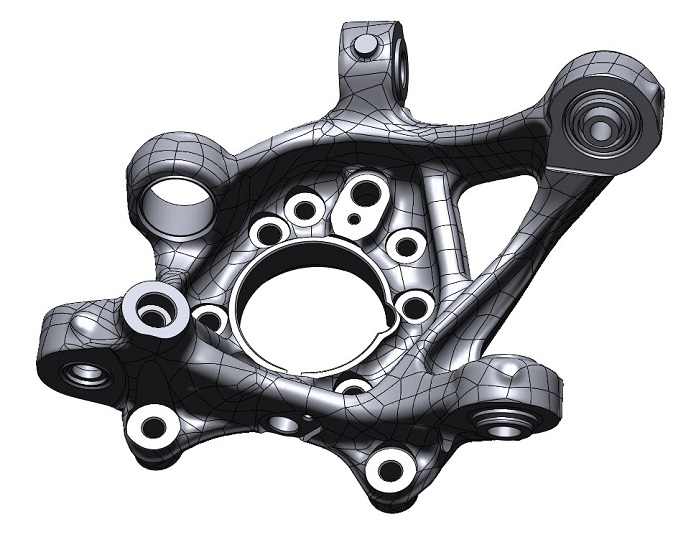
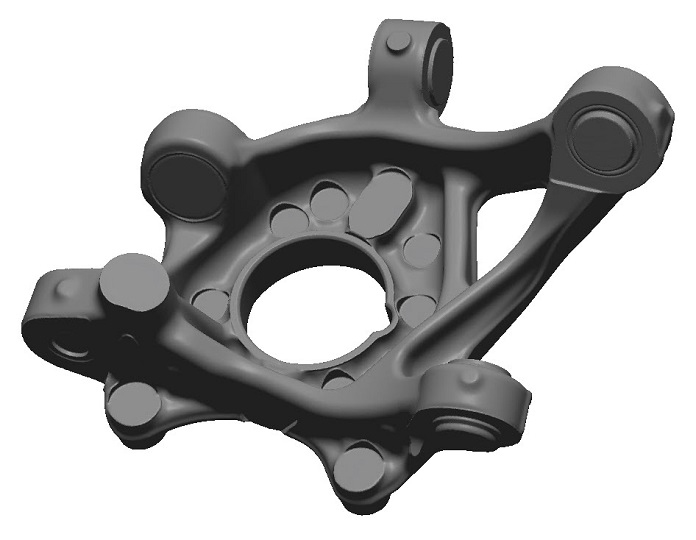
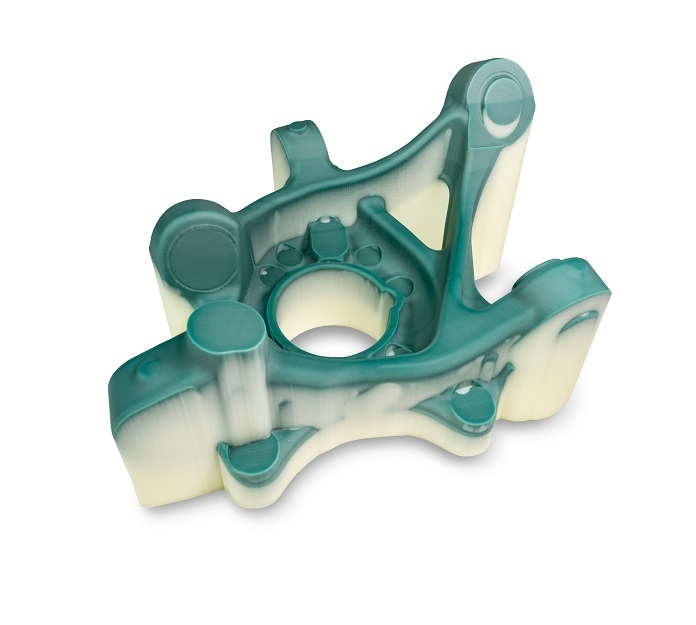
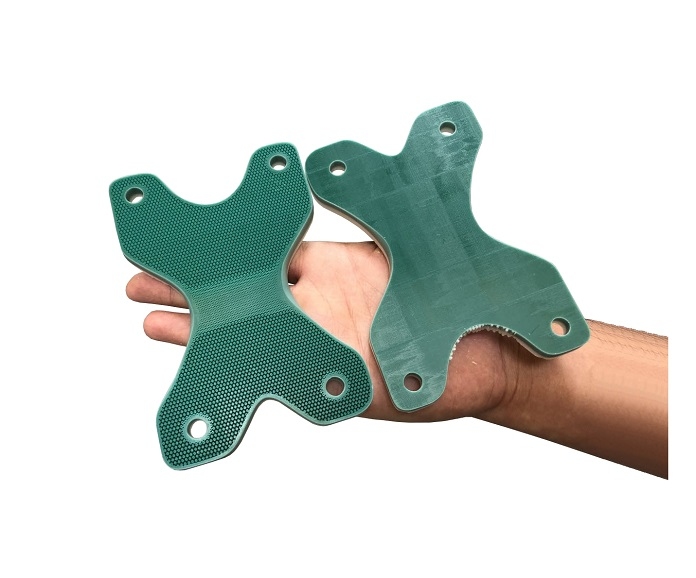
原始件扫描
混合CAD模型
用于打印的去特征模型
未完工的2500 IC打印件
Projet 2500 IC上样品横截面稀疏填充模式
模具制作
几十年来,增材制造在航空航天和汽车行业中被用于制作牺牲性铸件模具。由于近期3D打印技术出现新的进展,工业级模具能以极低的造价由蜡或高分子聚合物打印完成,能与脱蜡工艺无缝对接。如今,3D Systems已经更为广泛地应用于无工具增材模具制造,随着技术的普及、提速以及精准度的提升,将来这一应用还将更为广泛。
对涉及热能材料沉积的增材工艺或后期处理,可能会出现一定程度的沉积和“沉降”。质量较重的部件或重要截面区域存储热能的时间,会比轻薄型和小型部件更久。
基于这一认识,我们测试了两种打印方式,希望尽可能将打印材料的成本降到最低,同时保持最高水平的尺寸稳定性。我们测试了完全固体蜡打印法以及薄壳/稀疏蜡填充法,由3D Sprint Build客户软件准备,并在Projet MJP 2500 IC系统打印,最终生成蜡模。根据以往的经验,我们发现,当打印相对较大的零件时,带50%稀疏填充率的2毫米薄壳可产生高质量的稳定零件。
经过后期处理和冷却,我们使用同一台Artec Space Spider轻松扫描了两个模具。零件的独特形状、蜡的绿色以及后期处理的轻微钝化和增白效果,使我们的扫描技术人员能使用几何+纹理跟踪顺利捕获模型。
通过Geomagic Control X,我们直接导入了3D Sprint Build文件,并根据检验程序的打印方向检查了每个零件。因为我们将反复扫描主体部分来改善工艺,因此我们能够建立一个详细的检查项目并多次重复,同时将整个过程的开发历史记录保存在一个Geomagic Control X文件中。扫描完成后,我们只需将每个新的stl文件放入Control X项目中,评估过程就会自动进行,从而获得高质量、可重复的报告。
我们发现,通常所有带有加工偏移的区域都在铸件公差范围内,但自由度更高的区域有超出公差范围的趋势。我们认为,这与我们的假设有关,即大截面区域保留热量并在冷却时变形。
这一阶段的综合分析帮助我们得出一些结论,即带有蜡制模具的3D打印不仅更具成本效益,而且后期处理后,尺寸也更加合规。
浇铸
脱蜡法是一种可信赖的制造方式,其历史可追溯到5000年前,在工业革命后的几百年,它已在全球工业制造领域受到广泛认可。
如今,铸造工艺已相当成熟且极易重复,广为人知,模拟软件也涵盖了相关部分以减少内部零件出现缺陷的概率。与经验丰富的铸造厂合作,客户无需耗费额外精力,即可完成增材制造模具,并生产出没有内部缺陷的零件,表现超过普通工艺的铸模预期公差。
由于铸造工艺本身的稳定性,积极参与结果测试和工艺迭代测试的客户,在调整零件几何时,还能得到品质更高的产品。
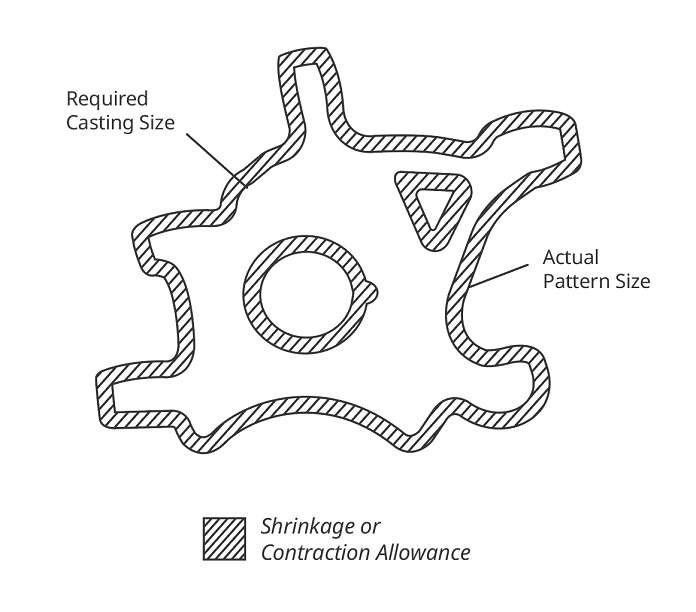
所需浇铸尺寸
实际铸模尺寸
• 工艺中零件物理用量减少约35%。
• 材料成本降低约27%。
• 整体公差合规性提升约10%(使用3D对比)
• 实体零件没有通过公差阈值。
• 填充零件通过公差阈值。
• 此外,进一步研究发现,室温下的尺寸长期稳定性高于实体零件。
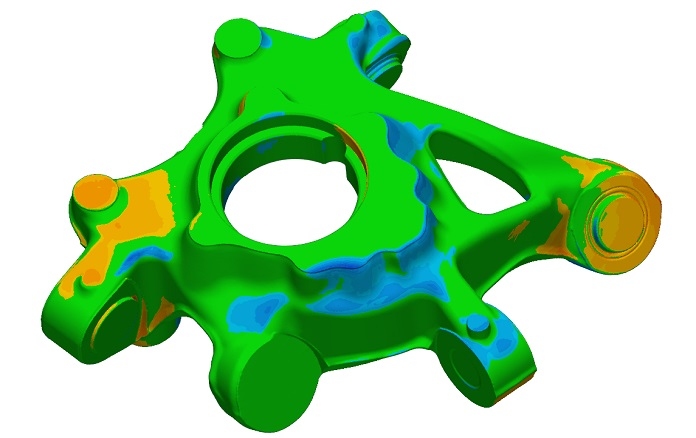
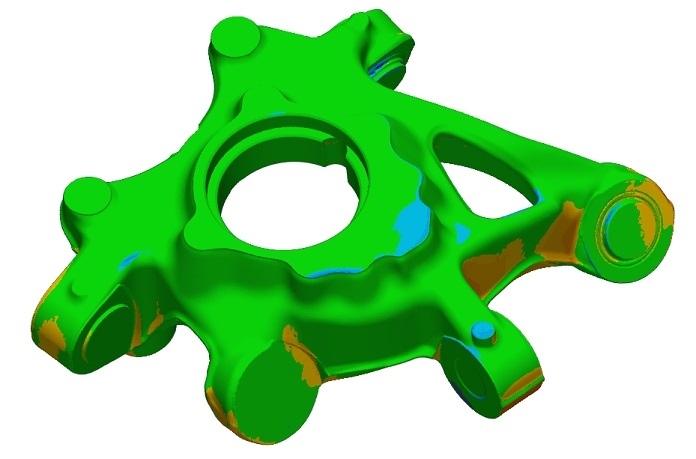
分析:实体蜡模具
分析:填充法蜡模具
收缩是铸造过程的常见结果,铸造厂通常会为客户提供一些指导,来弥补特定材料产生的收缩,用包围盒定义零件尺寸。由于几何复杂性以及物理浇铸过程的影响,通常大多数零件会出现不均匀的收缩。因此,铸造常常被视为“离散公差”的过程。
在转向节的铸造过程中,我们研究了适合模型和材料的收缩率。铸造厂建议使用2%的均匀缩放来生产准确的零件。为了研究3D扫描和精度缩放因子对成品精度的影响,我们按照建议的2%缩放因子制作了蜡模,并提供给铸造厂。
对返回铸件进行进一步检查,检查均匀的缩放因子是否符合预期公差。遵循常规铸模规范,一般零件肯定符合合作商规定的可实现的精度参数。但使用Control X中的“横截面”对比工具仔细检查发现,在某些明显部位,若更好地采用精度缩放因子,可大幅提升成品零件的整体精度。
根据严格公差进行的“横截面轮廓”对比,清楚显示了带有蓝色的外部边界,而内部边界则显示了橙色和红色。外部轮廓确认存在“尺寸过小”的情况,实际零件边界在参照边界内。内部轮廓显示,中心圆柱特征的尺寸小于预期,但出现在参照特征的外部。这表明,零件的总轮廓阴影存在缩放差异,可通过提高缩放因子、打印和再铸造来校正。
以往的铸造工艺改进研究让我们了解了如何对建议标准值进行调整,并将X、Y、Z轴调整为不均匀缩放因子,分别为2.2%、2.3%、2.7%,并再次打印了蜡模,提供给铸造厂。
通过对精度弥补模具的最终检查,我们得出有关模具到零件工艺的一些结论:
•精度缩放模具的结果超出了铸造厂的预期。
•缩放校正零件的整体尺寸合规性提升了约14%。
•随着精度的提高,可减少至少一次主加工工序。
•降低了零件总生产成本。
•可进行进一步分析,了解进一步提高精度是否可以减少整体加工工序。
结论
效率是维持利润、减少人工和生产周期中产生浪费的关键。借助Artec 3D Space Spider和Geomagic Control X,我们能够通过分析工业的每个阶段,来改善制造零件的总体质量,并尽可能减少调整周期和迭代次数。使用高质量3D扫描和扫描原生工业检查软件这一整体解决方案,可减少迭代和猜测,节省时间和金钱,并加快产品上市时间。
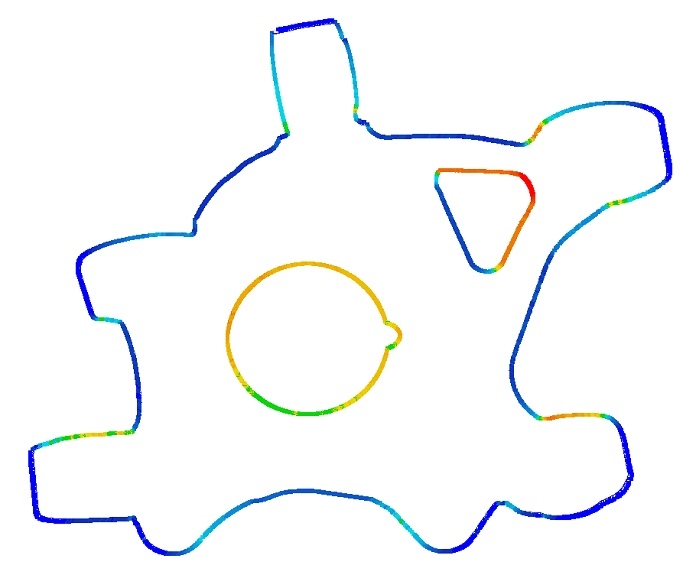
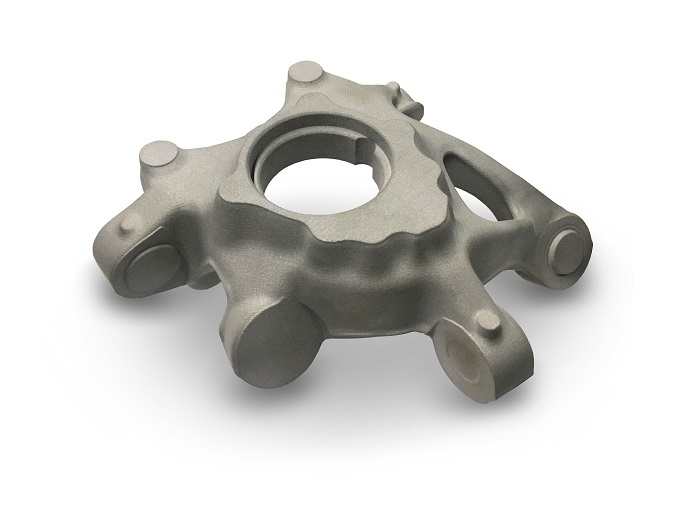
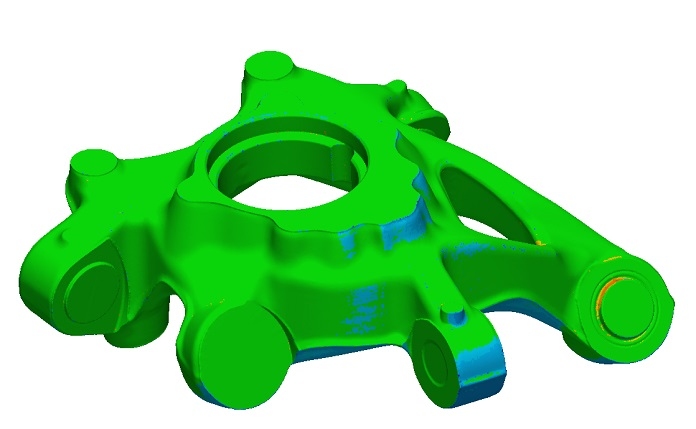
缩放误差截面分析
铸模零件成品
铸模成品分析
故事背后的扫描仪
尝试世界领先的便携式 3D 扫描仪。