数字化流程10倍增效货车大梁修复工艺,助力消除潜在事故风险
为什么选择Artec 3D?
作为100%无线且无需使用笔记本电脑的3D扫描仪,Leo可以在环境复杂的维修工厂进行扫描。对初学者来说操作简单,触摸屏可以随时查看扫描情况,大大提高现场采集效率。关键数据采集效率提升数十倍。

繁忙的货车长龙(来自网络)
自20世纪初汽车批量生产以来,汽车已成为人们生活中重要的交通工具之一,其中货车是现代运输和社会发展不可或缺的一部分。
据统计,截至2022年11月中国有约750万辆营运货车,超过2000万名货车司机,为全社会提供约四分之三的货运量和三分之一的周转量。
但是随之而来的公路交通事故及其所造成的人员伤亡和经济损失,经常给人们带来恐惧。尤其是货车事故,由于承载大量货物和视野盲区,一旦发生意外往往造成严重的后果。那么预防车辆风险,做好安全防护是避免悲剧的最好方法。
对货车结构充分了解的人都清楚,货车大梁是安全的重中之重,大梁就是我们俗称的车架,由悬挂装置的前后桥支撑在车轮上,它的作用是构成整个汽车的支撑结构,几乎承载了货车及其载重物的所有重量。比如汽车的发动机、悬挂系统、车身这三大部件都是靠它组成为一个整体,为汽车本身和驾乘人员提供安全保障。
大梁主要由纵梁和横梁组成,具体分为边梁式和纵梁式两种。货车大梁的材质基本上都是高强度的钢板,主要以铆接的方式连接从而组成钢性结构,这样才有足够的强度去承受车辆的负荷以及车轮传来的冲击。
一般情况下,大梁是不会变形的,若发生事故、侧翻会导致其变形,或长期使用、载重不平衡等也可能会导致其损坏,这就需要到专业维修机构矫正、加固甚至更换。
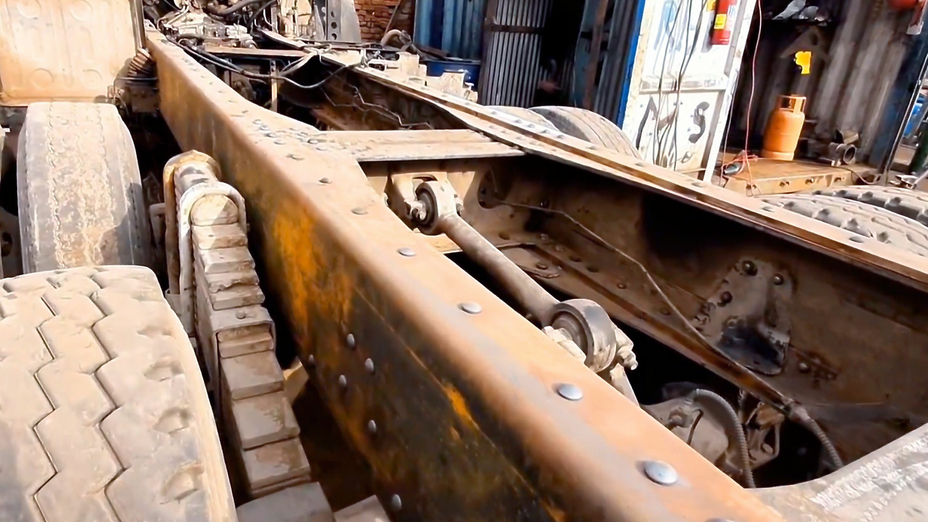
货车大梁(来自网络)
余姚九久汽车维修有限公司是一家专业从事机动车维修、配件、车厢制造业务的公司。迄今为止已经维修了超过2100辆货车,其专业度和维修效果备受客户好评。
因为车架的纵梁和横梁基本是通过铆焊接的方式连接在一起,在九久汽车的修理车间,维修师傅会通过液压机矫正变形的大梁。由于原货车大梁往往存在断裂和金属疲劳等因素,在矫正完毕后工人师傅会在内外侧加装高强度钢板来加固大梁来提高安全性。
大梁维修过程需要切割、焊接和以铆接的方式来放置定制部件,而无论是卡车司机还是九久汽车都没有这些大梁的原始CAD数据。以往的传统测量方法是用辅助工具测出原货车大梁的铆钉孔位置,然后在定制钢板上用传统的吸铁钻摇臂钻床完成上百个孔位的钻孔。
由于大梁很长且重,孔位数量多,尺寸不一,加固钢板的尺寸往往达到几米至十几米,整个过程操作困难、耗时长且不能保证精度。如果在安装时遇到孔位不准还需要调整,维修工期难以预测。
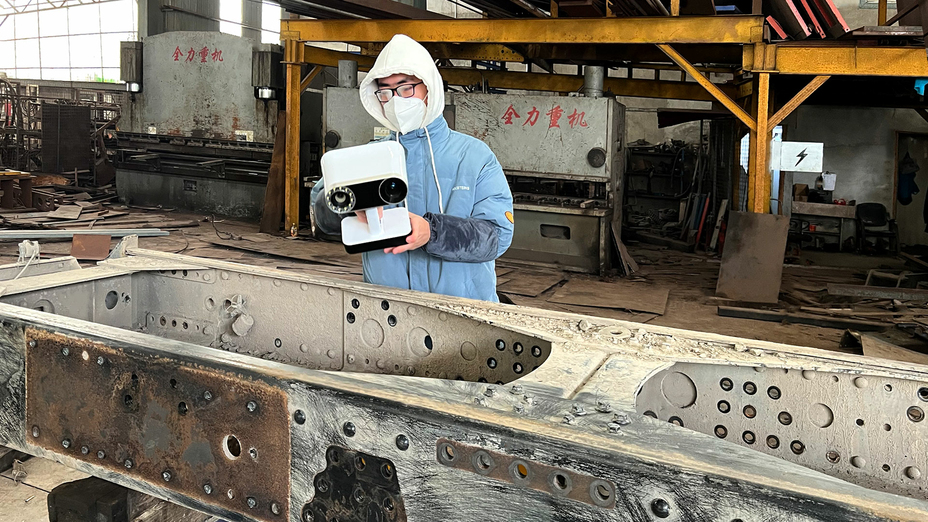
使用Artec Leo扫描货车大梁(宁波福莱德科技提供)
一次偶然的机会,公司管理层了解到Artec 3D的三维扫描技术。决定尝试新的方案来获取维修所需的数据,期待能优化大梁的修理流程。九久汽车联系到了位于中国宁波市的Artec 3D金牌认证经销商福莱德三维科技。
鉴于维修现场的实际条件和数据要求,福莱德科技的工程师首先推荐了Artec Leo作为首选解决方案。在维修工厂现场,工程师手持Leo,无需任何准备工作、也无需连接电脑的情况下花费了半个小时就完成了大梁的数据采集。
在扫描过程中工程师通过Artec Leo自带的触控屏可以实时查看采集的数据,随时调整,大大提高工作效率。
完成采集后,工程师把Leo捕获的原始数据导入Artec Studio 17中处理,生成完整的扫描数据并获得所有孔位的准确信息。
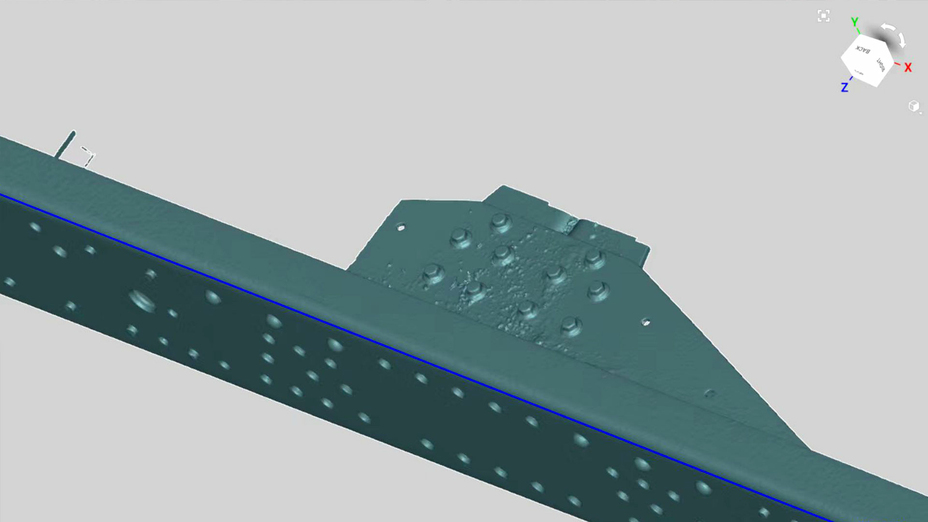
在Artec Studio中处理Leo采集的货车大梁数据(一)
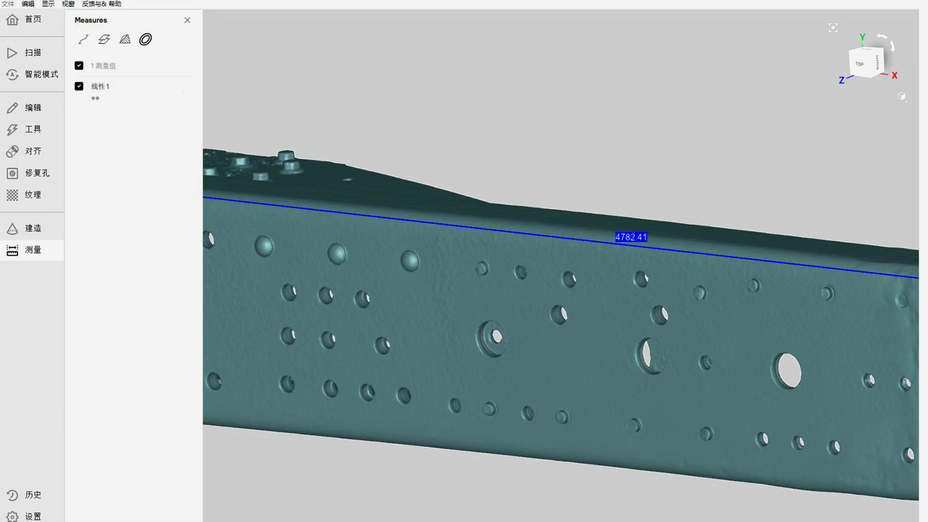
在Artec Studio中处理Leo采集的货车大梁数据(二)
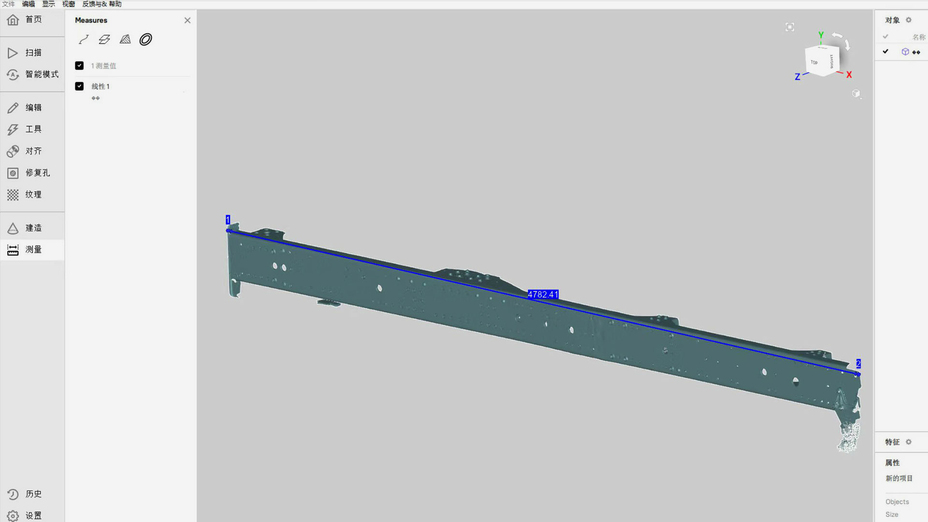
在Artec Studio中处理Leo采集的货车大梁数据(三)
在Artec Studio中处理完毕后,工程师把大梁的数模导入到Geomagic Design X中进一步逆向建模以得到参数化模型,并在该模型基础上生成参数化二维图。
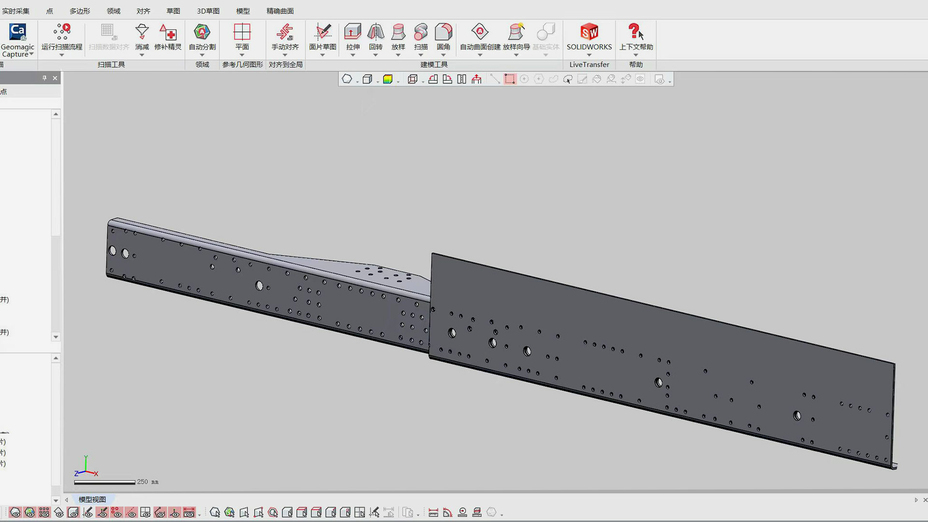
在Geomagic Design X中逆向建模货车大梁,生成参数化模型
工艺的最后一步是将获得的参数化二维图文件导入激光切割机,自动完成对钢板的所有定制化切孔。
九久汽车在体验了全部流程后感到十分满意,新的工艺流程不但减少了人工操作还提高了最终件的孔位精度,在铆接的过程中所有孔位都匹配良好,减少了维修时间和可能的返工成本,为扩大业务提供了前提条件。

安装完毕的加固钢板(外侧),图片由九久汽车提供
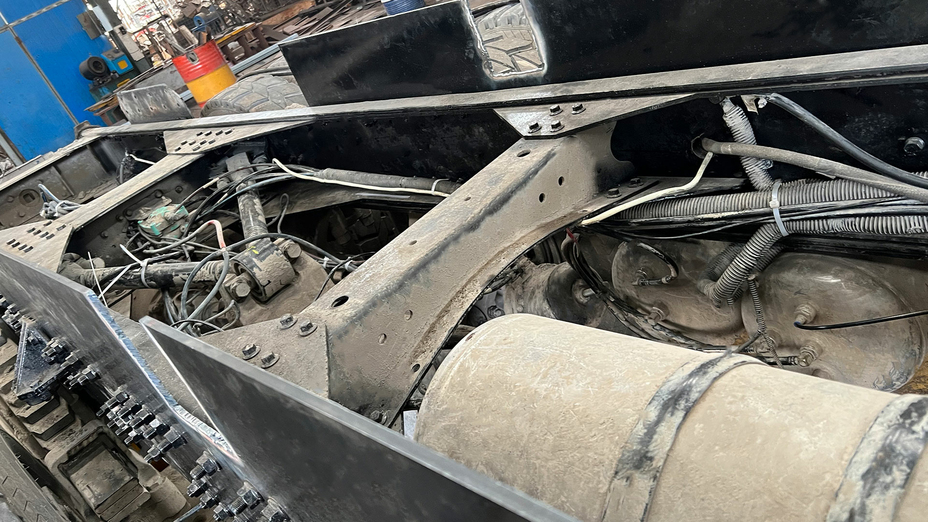
安装完毕的加固钢板(内侧),图片由九久汽车提供
九久汽车创始人吴富强说:“使用Artec Leo的三维扫描技术后,我们的维修效率有了大幅提高,我们正在更多的应用场景中尝试新技术来帮助其他相关业务。”,Artec 3D在制造业尤其是逆向工程领域以其完整、易用、高质量的解决方案助力用户达到期望的目标。
故事背后的扫描仪
尝试世界领先的便携式 3D 扫描仪。